阀座零件的材料为牌号LY12的铝合金,其结构如图1所示。在加工阀座时存在以下主要加工难点:
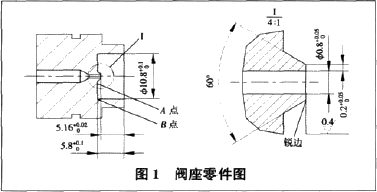
1、0.2
+0.050mm平台处粗糙度R
a0.4um,在40倍显微镜下检查表面无缺陷。
2、0.2
+0.050mm平台与!0.8
+0.050mm内孔交接处保持锐边。
3、深度尺寸5.16
+0.020mm难以保证。
一、阀座主要加工难点的分析
由于没有合适的标准刀具,采用了手工磨制硬质合金刀具。精加工内腔时,刀尖需要从内腔中心走到0.2mm小凸台以及锥度底端,因受制于内孔!10.8
+0.10mm,刀体宽度受到限制,经计算,孔内60°锥台底端处宽度尺寸为4.33mm左右,也就是说刀体宽度必须小于锥台底端处宽度4.33mm,因而刀体强度低,刚性差,再加上磨制时刀尖容易崩刃,前角不易磨得很锋利,磨制后在工具显微镜下修磨出刀尖圆弧尺寸,不容易控制。在实际加工中,Ra0.4!m粗糙度很难达到要求,5.16
+0.020mm深度尺寸因每一次刀尖状况不一样和中心处与外端面线速度不同而产生波动,最大要补偿0.02mm左右,而且不稳定,加工过程中随时可能变化,要经常测量调整。0.2
+0.050mm平台和Ø0.8
+0.050mm内孔交接锐边处容易出现毛刺。每一批次加工时均需修磨刀尖,首件加工时反复调整刀具尺寸参数,而且加工过程中不可靠,经常要到显微镜下观察监测表面状况,操作难度大、不容易控制、加工效率低、返修率高。
分析产生以上现象的主要原因是精加工手工磨制刀具刚性差、刀尖处不锋利、刀尖不耐用。
二、刀具的设计
1、确定刀具的结构
为解决精加工刀具刚性差的问题,采用Ø8mm圆刀杆,且把刀尖放在Ø8mm圆刀杆中心轴线上,Ø8mm刀杆便可进入Ø10.8
+0.10mm内孔中,即使刀尖从内腔中心至0.2mm小凸台以及锥度底端,Ø8mm刀杆也不会与Ø10.8
+0.10m内孔相干涉,因为小凸台高度最大只有0.74mm,所以刀尖只需伸出2mm左右就足够了,这样刀杆的刚性将得到大大提高。
2、刀片的设计
为了使产品质量稳定,在加工过程中尽可能的少调整,减少监测,提高加工工艺性,经过反复比较,选用肯纳公司CPEX060201L1KM1型号镗刀片进行改制,原始刀片尺寸和改制后刀片尺寸见图2和图3。
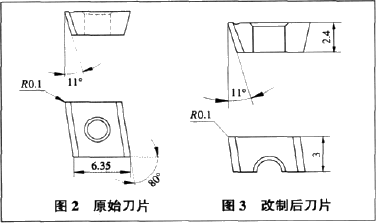
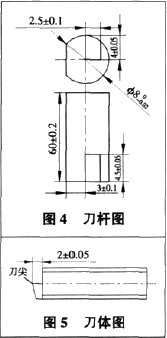
此种刀片用线切割机床切开后宽度为3mm,刀尖可以进入锥度底端A点和B点,刀片前角10°,后角11°,刀尖圆弧0.1mm,刃口锋利,刀尖圆弧标准,便于安装。此刀片适合铝合金的加工。
3、刀杆与刀体设计
制作Ø8mm刀杆(材料45钢)与刀片结合为一体,刀尖在刀杆中心轴线上,刀杆图和刀体图见图4和图5。由于改制后刀片只有半圆形螺钉孔,刀片装在刀杆槽上,无法靠螺钉压紧固定,于是选用丙烯酸脂胶HL-302填充缝隙空缺。因在精加工时只有0.05mm左右余量,切削力、刀片的粘结力足够,粘结牢固。
4、刀具的安装
刀具安装在数控车床上,装刀系统为刀塔式,4个刀位,在实际使用时,出现刀位不够的情况。制作刀架来解决此问题:精磨刀架的安装定位面,使其与刀具安装面接触良好,在数控车床上配钻2个Ø8mm的刀具安装孔,保证其准确的位置和重复安装精度。刀架图见图6。
三、应用效果
实际加工时,刀杆刚性良好,刀片强度好,刀刃锋利,准备时间大大缩短,效率显著提高,保证了产品质量,加工上千件产品,刀尖状况良好,首件调整合格后,一批几百件的工件基本不用调整和监测。在生产中类似阀座的几种零件相同的加工难点也一并得到了解决。
四、结论
实践证明:该刀具的结构简单、合理、使用方便、装夹与定位简单可行、耐用度好。改善了加工者的劳动条件,极大的提高了劳动生产率,同时保证了产品质量、降低了加工成本、提高了经济效益,在实践运用中值得推广借鉴。
(1)陆剑中,孙家宁。金属切削原理与刀具(M)。北京:机械工业出版社,1999。