我们知道任何的
调节阀都是不允许有外漏现象发生的,而发生外漏的主要途径之一是介质从阀杆处外泄,为了防止上述情况的发生一般采用了填料密封,即在阀杆处用
填料函密封,如图1所示。
其密封原则是根据使用工况填料4在压盖2的压力作用下产生一定的径向力,使其紧密与阀杆1和阀盖3接触,从而防止液体或气体等介质外泄。
一、填料密封主密封压力的计算
如上所述,通过拧紧压盖2上的螺栓对填料函(即阀盖)3内的填料4进行轴向压缩,填料的塑性使其产生径向力并与阀杆1紧密接触。同时,填料中添加的润滑剂被挤出在接触面间形成油膜。由压力分布示意图于接触状态不均匀,接触部位出现边界润滑状态,未接触的凹部形成小油槽有较厚的油膜。当阀杆1与填料4有相对运动时,接触部位与不接触部位组成了不规则的迷宫阻止了介质的泄漏。
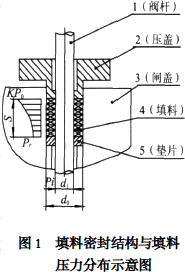
为了保证填料密封的可靠性,必须保证填料对阀杆的径向压力即主密封压力。根椐填料密封时的压力分布理论分析和各种填料设计的性能测试,得出填料的径向压力即
主密封压力计算式:

式中P
r为填料径向压力(MP
a);P
0为填料压盖处轴向压力(MP
a);K为填料压力比(又称应力系数);d
1为阀杆直径(mm);d
0为填料函孔径(mm);s为填料深度(mm);μ
1为填料与阀杆间的动摩擦因数;μ
2为填料与填料函间的静摩擦因数。
填料压力比是填料径向压力与轴向压力之比,是确定填料高度的一个重要因素。应力系数K取决于轴向压力,如图2所示。
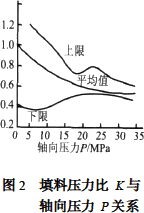
. 填料密封时的压力分布情况如图1所示,可见,填料最大径向压力P
rmax在填料4与压盖2接触处,随着填料4高度的增加,径向压力Pr按指数规律降低,所以最小径向应力P
rmin在填料4与垫片5接触处。为避免此处发生泄漏,根椐式(1),计算得到P
rmin,该值应大于等于
阀门内部介质压力P
i。
二、填料密封分析
对填料密封的有效密封条件是采用适当的填料函形式和填料,分述如下。
1、填料的选择
对填料的要求是要有一定的塑性,在轴向压力的作用下能产生一定的径向压力,要有抵抗温度变化的能力,有抗蠕变,抗松驰等能力。此外,还要有足够的化学稳定性,抗氧化能力,不污染介质,不被介质泡涨,不腐蚀阀杆,摩擦因数小。且在阀杆有少量偏心时,填料应有足够的浮动弹性。填料本身应制造简单,填装方便。目前使用的填料一般有石棉石墨填料、柔性石墨填料和聚四氟乙烯填料。其特性及应用场合见表1。
2、填料密封中摩擦力的影响
据主密封压力公式(1),如果μ
1+μ
2(d
0/d
1)=0,则填料顶部施加的轴向压力P
0能均匀地传递到整个填料深度而没有任何衰减。但由于摩擦的存在,径向压力P
r随着与压盖2距离的增加而减小。摩擦越大,径向应力P
r衰减得越厉害,所以摩擦因数μ
1和μ
2应尽可能小。此外,d
0/d
1总大于1,所以在减小应力衰减的作用上,μ
2比μ
1更重要。
阀杆1表面和阀盖3内孔表面粗糙度对阀杆处的密封和磨损至关重要。阀杆1与阀盖3内孔的表面粗糙度应尽可能小,一般阀杆表面R
a≤0.8μm,阀盖3内孔R
a≤1.6μm。
3、填料函内孔直径与填料截面宽度
根据填料密封主密封压力方程式(1),填料函孔径和阀杆直径的比值d
0/d
1,也影响着径向压力P
r的大小。而对于不同的阀杆直径d
1,填料的截面宽度S=(d
0-d
1)/2,存在一个得到最佳密封性能的范围,一般经验公式取S=(1.2~1.5)

,即d
0=(2.4~3.0)
4、填料的选择与安装
填料的选择或安装不合理,同样可以导致阀杆密封泄漏,为确保填料密封性能,应采用以下措施:1)除硝酸、浓硫酸等强氧化性介质外,可选用柔性石墨,并在柔性石墨上部及下部均使用一圈石棉编制绳。该种密封填料可增加填料强度,并可防止填料挤出,增加填料密封的密封性。
2)阀门解体后,最好装入不切口的整环盘根(即图1中的填料4)。因种种原因而必需装入切口盘根时,盘根接头切口应切成45°,各层接头应错开180°,且填料压盖2不得倾斜,并留有足够的再压余量,使整个填料组件4被压缩30%。填料压盖2上的压套压入填料函的深度为其高度的1/4~1/3。
3)高温
高压调节阀门应控制填料压盖螺栓转矩,若螺栓与螺母均处于洁净良好的润滑状态时,可以通过系统压力、填料尺寸、螺栓大小和旋入螺纹数等来估算螺栓的预紧转矩,为填料的压缩量提供依据。
三、结论
要达到良好的阀杆密封效果,就必须根椐不同的工况条件选择适当的填料材料,合理设计填料函深度及阀杆直径、采用合理的填料密封结构。