WCB铸钢是以碳为主要强化元素的钢种,具有良好的可靠性和安全性,而且可焊性较好,目前广泛用于寒冷地区的
调节阀铸件上。本文将探讨通过合理的控制成分和熔炼工艺,获得优质的钢液。
一、化学成分的选定
1、碳
在碳钢中,w(C)≤0.18%时,低温α
k值随C含量提高而增加。w(C)≥0.18%后,随C含量提高,α
k不断下降。但C含量过低的钢(w(C)<0.18%),因其中珠光体量减少,而且w(C)<0.20%铸件热裂倾向大,抗拉强度随w(C)升高而增加,屈服强度上升至0.3%时趋于平缓,伸长率和断面收缩率随w(C)升高而急剧下降,因此以抗拉强度与屈服强度满足最低标准为保证,WCB钢又有较好综合力学性能,选w(C)=0.25%~0.28%。
2、硅
Si是作为脱气剂加入的,它能还原FeO,从而消除FeO夹杂对钢的不良影响。低C钢中的Si大部溶于铁素体中,有助于提高钢的强度。在WCB钢生产中,一般控制w(Si)=0.45%~0.55%。
3、磷与硫
磷与硫对WCB钢低温A
K值影响大。随着钢中P、S含量的提高,低温A
K值急剧下降。磷在组织中析出化合物F
e3P,使钢的脆性提高,硫在钢中与Fe生成化合物FeS,FeS与Fe又能形成低熔点共晶体,使钢的脆性加大。在生产中将P、S控制得越低越好。通常P控制在0.04%以下,S控制在0.045%以
下。
4、锰
Mn与S生成MnS,呈点状分布于晶界上,有一定塑性,Mn还可细化晶粒,有助于改善低温α
k值。故生产中常把Mn控制在w(Mn)=1.0%以下。
二、熔炼工艺
采用0.5t中频电炉熔炼,碱性炉衬,选用一般用途废钢(C≤0.12%),S、P质量分数各小于等于0.05%。废钢表面去油污、锈等杂物。首先在炉内加入适量增碳剂。开始通电时,给60%左右的功率,待电流冲击停止后,逐渐将功率增至最大值。随着坩埚下部炉料熔化,随时注意捣料,防止“搭桥”,并继续添加炉料。大部分炉料熔化后,加入造渣材料(石灰粉∶萤石粉=2∶1)覆盖钢液,造渣材料加入量为1%~1.5%炉料熔化后,取1号试样分析C、S,并将其余约总量5%的炉料加入炉内。炉料熔清后,将功率降低至40%~50%,倾炉扒除全部炉渣,并补入渣料另造新渣。渣料化清后,在渣面上加脱氧剂,进行扩散脱氧,脱氧过程中可用石灰粉和萤石粉调整炉渣粘度,使炉渣具有良好的流动性。加入硅铁和锰铁进行脱氧,取样分析结果,调整钢液化学成分。用光电温度计和热电偶相结合测定温度。并作圆杯试样,检查钢液脱氧情况,钢液达到1640℃,圆杯试样收缩良好时准备出钢,用0.08%铝丝放入包底进行终脱氧,停电倾炉出钢,出钢后在盛钢桶取样,作成品钢液化学分析,钢液镇静3~5min后浇注。每炉检测初浇温度、中间温度、终浇温度,测得试样的化学成分和力学性能如表1、图1和图2。
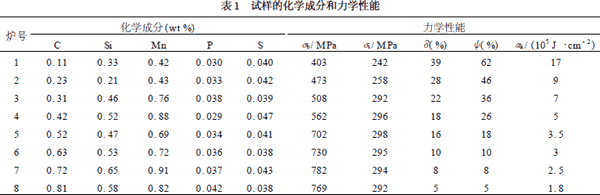
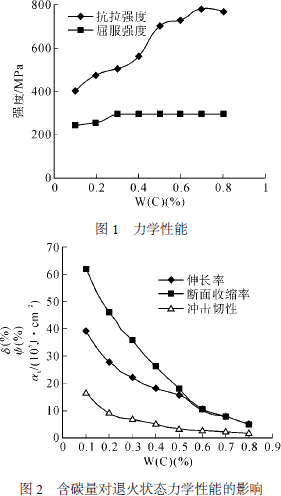
废钢材料应洁净、干燥,否则会渣多气大。造渣要充分,并且要及时扒渣,化成钢液后在表面覆盖一层造渣材料或干砂,隔绝钢液与空气,除气是熔炼的关键,1
#和2
#两炉钢液浇注树脂砂型,均出现严重的呛火,从化验成分看,含硅和锰未达到预期值,说明大部分硅和锰与氧结合形成渣,而钢液中气还未除尽造成呛火,发现这两炉加入硅、锰是在出炉前20min,并且熔炼时钢液有沸腾现象。后改为出炉前7min加入第二份硅、锰铁,再无呛火发生。
三、结论
铸造WCB钢的力学性能主要受碳影响,因此要调整好碳含量。熔炼工艺的重点是钢液脱氧,因为脱氧不良造成钢液[FeO]、[MnO]过多,降低了钢的强度、塑性、抗热裂的能力,氧化严重的钢液流动性差,在铸件表面易产生氧化物,在浇入树脂砂型腔内出现呛火等,在熔炼时除用硅铁、锰铁脱氧外,临出炉时再用铝终脱氧。控制渣中w(Fe)<0.5%,FeO和MnO二者总量≤1.2%。