四、调节阀口径的计算与选择 4.1 调节阀口径的选择步骤 在已知工艺生产流程,确定阀的控制对象和使用条件,按
调节阀选型原则选定阀的种类型号和结构特性以后,就可以进行下一步选择调节阀的口径。调节阀口径的选择步骤如下:
(1)根据工艺的生产能力设备负荷,确定计算调节阀流通能力的最大流量、常用流量、最小流量、计算压差等参数。
(2)根据被控介质及其工作条件选用计算公式,确定流体介质密度、温度、粘度等已知条件井换算到工作状态下,然后代入公式计算出流通能力K
v。而后按阀的流通能力应大于计算流通能力的原则,查阅生产厂提供的资料,选取调节阀的口径。
(3)根据需要验算开度或开度范围、可调比R等。
(4)计算结果若满意,则调节阀口径选定工作完毕。否则重新计算、验算。
调节阀的流通能力,是指调节阀上的压头损失一个单位时,流体通过调节阀的能力。
阀门的流通能力也称
流量系数K
v。如今国际规定:温度为5℃至40℃的水,在105P△压降下,1小时内流过调节阀的立方米数。
关于流量系数即调节阀流通能力的计算,各类书刊介绍颇多.上海工业自动化仪表研究所编写的《调节阀口径计算指南》(以下简称《指南》)已有详细的论述。《指南》是我国调节阀口径计算的准标准,很有权威性,它将介质流体分为不可压缩流体可压缩流体和两相流3种对象,根据不同介质选用不同的计算公式。《指南》给出了详细的计算步骤,并提供了各种流体介质的计算实例,甚至实现了计算机程序化计算,本文不再赘述。选择正确的计算公式,合理确定计算流量和计算差压是很重要的,不然将导致调节阀口径选择不当。
4.2确定计算流量 调节阀口径计算的流量,应是系统工作的最大流量Q
max,也就是调节阀最大开度时的流量Q
100,该值是由工艺设计人根据设备的生产能力、物料平衡、控制对象的极限负荷变化,以及预测的可能扩大的生产能力与操作条件变化等因素,综合考虑后确定的。
通常,取正常操作流量的1.3~1.5倍作为计算的最大流量较为合适。过大,势必使阀径选择过大,这将使得调节阀经常处于小开度工作状态。可调节范围显著减小,动作频繁,阀的调节特性变环,严重时则影响调节系统的稳定性和阀的寿命;过小则形成瓶径,不能满足生产上对流量的需要。
设计中如果必须考虑富裕量时,阀径可以选得稍大一点,但在近期时应使阀的开度不小于40%~60%。对分期建成的工程,不能用最终规模的流量作为计算流量。因此,在设计中应积极协助工艺合理确定计算流量,为正确计算,合理选定阀径创造条件。据调查,设计中选定的阀径,偏大的情况占多数,由此造成调节系统不稳定甚至失灵的后果履见不鲜。设计者应该反复推敲,合理确定计算流量,这一点很重要。
4.3确定计算差压 进行调节阀口径计算时要确定最大流量时阀前压力P
1和阀后压力P
2,这样P
1-P
2=△P就是计算差压。△P这个参数选定直接影响计算结果,工艺专业往往未经深思熟虑就给出P
1和P
2。当然,这也是一个较难确定的参数,在设计时应该积极配合工艺专业,合理确定计算差压,阀前后压差选定极大地影响调节阀的工作特性。调节阀的工作特性实际上取决于调节阀的压降与管路系统总阻力损失的比,这个比值S越大,阀的特性就越接近F理想;但是S值过大时将会使阀上阻损过大,增加能量的损耗,因此,确定调节阀压降是十分重要的。压降△P
v的选定方法,根据不同的已知条件有多种,现介绍常用的几种方法如下:
(1)按管路系统的阻损比来确定△P
v 所谓阻损比S,就是在调节阀全开时,阀上的压降△P
v与管路系统各局部阻力件压降之和∑△P
1加阀的压降△P
v的总和的比S,其数学表达式:

(4-1)
整理后,得计算差压为:

(4- 2)
所谓铸路系统的局部阻力件,即管段、弯头、三通、手动阀门、节流装置等等。∑△P
1一般由工艺专业提供,也可以按下式求得:

(4-3)
式中:ε为阻力系数,可查阅管道专业的阻力系数图表;
v为流速m/s;
ρ为流体密度g/m
3;
△P
1为阻力损失kPa。
s值的大小与调节阀的工作特性有密切关系,当S=1时系统总阻损几乎全部集中到阀上,随着S值的减小,不仅阀在全开时流量减少,而且
流量特性也发生变化,可参考表1。因此,—般工程设计中,不希望S<0.3,常用范围S=0.3~0.7,最好在0.5左右。对于密闭容器有静压波动的场台,考虑到系统背压波动会直接影响阀上压降的变化,使S进一步减小,如锅炉给水自动调节系统,在计算压降△P
v时,还直增加5%~10%的系统背压,即:

(4-4)
关于管路系统的选定,一般取调节阀前后最靠近阔的两个定压点之间的一段管路作为系统的管路。所谓定压点,即该点压力不随流量变化而变化。例如,阀前的介质总管、车间总管、风机出口等,阀后的炉膛压力、喷嘴前压力等一般来说是不变的。
(2)按定压点的压差选取阀的压降
在初步设计时,由于工艺管路尚未具体确定,这时局部阻力形式还不知道,按上述公式(4-2)、(4-3)计算是有困难的,但阀前后的定压点一般是可以确定的。
设P
1为阀前定压点压力,P
2为阀后定压点的压力,则:
∑△P
j+△P
v=P
1-P
2 (4-5)
代入上述公式(5-1),得:
△P
v=S(P
1-P
2) (4-6)
(3)如果已知原动机(风机,泵等)的特性和管道系统的阻力变化特性,如图(4.1)。
如上图调节阀前后压降可由F式求得:
ΔP
v=P
Amin- P
Bmax (4-7)
式中:
P
Amin为原动机在给定流量时的最小压力;
P
Bmax为管路系统在给定流量的最大压力损失。
(4)对f要求阀后保持恒压的系统,如已知管路中可能的最小压力P
1min和调节器的压力整定范围P
Tmin~P
Tmax则可取:
ΔP
v=P
1min- P
Tmax (4-8)
(5)对于放空调节阀压降的选取
对于气体管道中的放空调节阀,在正常情况下,放空是全闭的,阀前的压力为P
1,它与管网的压力一样。阀后的压力P
2是大气压。但阀全开后,阀后的压力P2就与放散的流量有关。放散量随阀后阀前的压力比P
2/P
1的大小而变化。当P
2/P
1=1时,放散流量等于零,随此比值的减小,流量增大。当达到某一所谓临界压力比时,流量将达到最大值,继续减小压力比时,流量将保持此最大值不再改变。放空调节阀多数用于保护性装置,希望在短时间内达到最大的放空量。同时还要使所选的阀能起到调节作用,并且尺寸的大小还要符合经济的原则。因此,在选取计算压降△P
v时,根据临界压力比来确定是比较合理的。
临界压力比对于不同的气体有不同的值,对于空气或双原子气体,临界压力(P
2/P
1)L=0.528其它气体的临界压力比,可以参考表2。
表2 气体的临界压力比值表
序号
| 气体介质名称
| 多变指数K
| 临界压力比P2/P1
|
1
| 单原子气体
| 1.667
| 0.498
|
2
| 双原子气体
| 1.400
| 0.528
|
3
| 原子气体和过热水蒸气
| 1.300
| 0.546
|
4
| 饱和水蒸气
| 1.135
| 0.378 |
根据临界压力比计算选取阀的压降,可按下列公式计算:
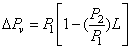
(4-9)
这时阀后的压力P
2=P
1(P
2/P
1)L,用以克服放散管的阻力和气流冲向大气的动力。其装置的原理如图(4-2)。
(6)对于现成的管路系统,如果需要设计安装调节阀,在计算调节阀径时,最好先测出最大负荷。手动球型阀前后的压力P
1和P
2。计算压降则如下式求得:
△P
v=P
1- P
2 (4-10)
以上是几种常用的确定计算差压的方法,当然对于不同的工艺对象还有其它的确定计算差压的方法,请设计者参考有关书刊的经验介绍,也可以参照上述情况举一反三。
当合理确定计算流量和计算差压之后,则还要仔细查阅一些流体介质的物理性质图表。选择一些辅助参数。而后按步骤进行阀径计算来确定调节阀的选型。
五、结论 调节阀设计选型计算是一项技术性很强的工作,要想使调节阀设计选型的结果符合现场的实际需要,必须做许多深入细致的工作。特别强调的一点是,调节阀的设计选型不仅是自动化仪表专业的事,设计选型是否合理与工艺专业关系极大。因此设计选型时,要主动积极地取得工艺专业的配合,这样才能有比较好的设计。作为自动化仪表专业在工程设计中需尽可能地了解工艺流程,掌握各种生产流程对控制系统调节阀的具体要求,要判断其是否切实可行,要变被动设计为主动设计。通过科学的分析,合理选择计算参数,而后精心设计计算,并验算调节阀的选型。有时,还要进行力矩或推力的计算。当设计完成之后,在施工调试时要进行技术跟踪,通过实践来检验设计选型的结果是否合理。要密切与现场工人相结合了解调节阀的运行情况,不断的总结经验与教训,努力提高我们的设计水平。
参考文献 1、上海工业自动化仪表研究所.奚文群,谢海维.调节阀口径计算指南
2、清华大学工业仪表及自动化教研室编制.过程控制系统讲义